Dr Kirsty Hewitson, Director of RACICo
All the above have passed through the ESS and UKAEA’s quality assurance requirements. This shows the power of collective thinking and collaborative working. RACE’s functional safety capability can be applied in fusion, fission, and big science areas.
RACE now has a Functional Safety Group of seven people who support ESS and the wider RRDD (Robotics, Repurposing & Decommissioning Directorate) portfolio.
Michael Van De Mortel, Head of Operations, RACE Electrical Engineering Unit, said:
“This is a UKAEA first, delivering a complex nuclear safety system which will support the ESS operational safety case to the Swedish Nuclear Regulator.
”I want to commend and congratulate everyone involved in the successful delivery of the recent ESS Radiological Safety System SAT (Site Acceptance Test) as well as those who have supported over the years. The professionalism and technical knowledge was extremely well received by the stakeholder.”
RACE is the systems integrator for the ESS’ Active Cells Facility and has now successfully delivered the Radiological Safety System Site Acceptance Test, which supports the ESS operational safety case to the Swedish Radiation Safety Authority.
The ESS is a multi-disciplinary research facility in Lund, Sweden and will be the world’s most powerful neutron source, enabling research in materials, energy, health, and the environment.
RACE did not have any functional safety capability when this journey started and this major milestone represents eight years of hard work and overcoming challenges; growing through engaging and learning from industry, self-delivery learning and training. Many of the challenges could never have been comprehended at the initiating HAZOP (Hazard and Operability Study) workshop in 2016.
Radiological Safety System Facts & Figures
30,000hrs of resource time
£1m hardware procured, manufacture, installed and commissioning at ESS site
Contract management with a functional safety consulting company
30 substantiation documents (2000+ pages)
1,000 pages of drawings
20 cubicles
12km cabling
2km of cable managements systems
4,000 components
10,000 electrical connections
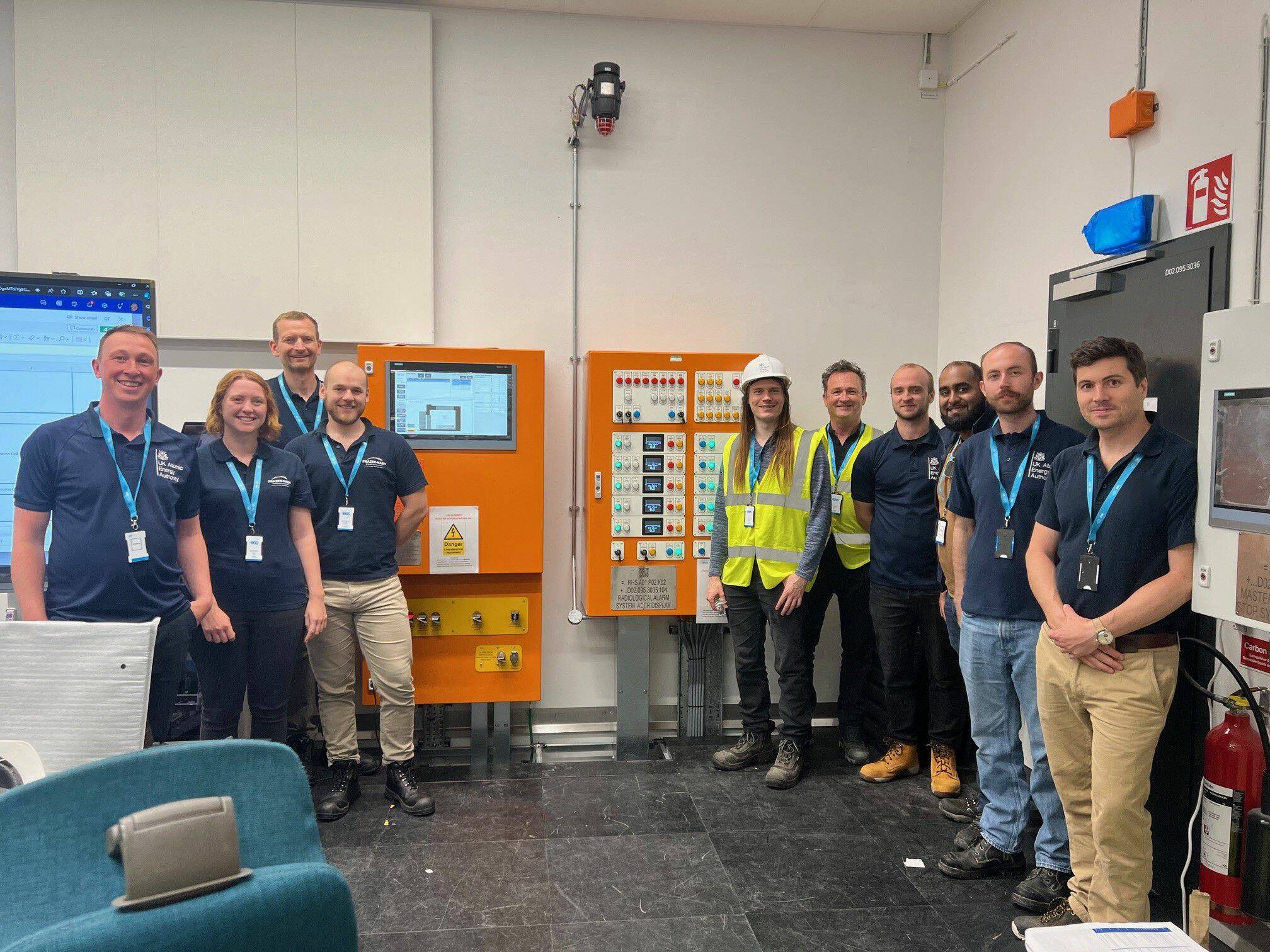
Radiological Safety System Facts & Figures
30,000hrs of resource time
£1m hardware procured, manufacture, installed and commissioning at ESS site
Contract management with a functional safety consulting company
30 substantiation documents (2000+ pages)
1,000 pages of drawings
20 cubicles
12km cabling
2km of cable managements systems
4,000 components
10,000 electrical connections
All the above have passed through the ESS and UKAEA’s quality assurance requirements. This shows the power of collective thinking and collaborative working. RACE’s functional safety capability can be applied in fusion, fission, and big science areas.
RACE now has a Functional Safety Group of seven people who support ESS and the wider RRDD (Robotics, Repurposing & Decommissioning Directorate) portfolio.
Michael Van De Mortel, Head of Operations, RACE Electrical Engineering Unit, said:
“This is a UKAEA first, delivering a complex nuclear safety system which will support the ESS operational safety case to the Swedish Nuclear Regulator.
”I want to commend and congratulate everyone involved in the successful delivery of the recent ESS Radiological Safety System SAT (Site Acceptance Test) as well as those who have supported over the years. The professionalism and technical knowledge was extremely well received by the stakeholder.”
RACE is the systems integrator for the ESS’ Active Cells Facility and has now successfully delivered the Radiological Safety System Site Acceptance Test, which supports the ESS operational safety case to the Swedish Radiation Safety Authority.
The ESS is a multi-disciplinary research facility in Lund, Sweden and will be the world’s most powerful neutron source, enabling research in materials, energy, health, and the environment.
RACE did not have any functional safety capability when this journey started and this major milestone represents eight years of hard work and overcoming challenges; growing through engaging and learning from industry, self-delivery learning and training. Many of the challenges could never have been comprehended at the initiating HAZOP (Hazard and Operability Study) workshop in 2016.
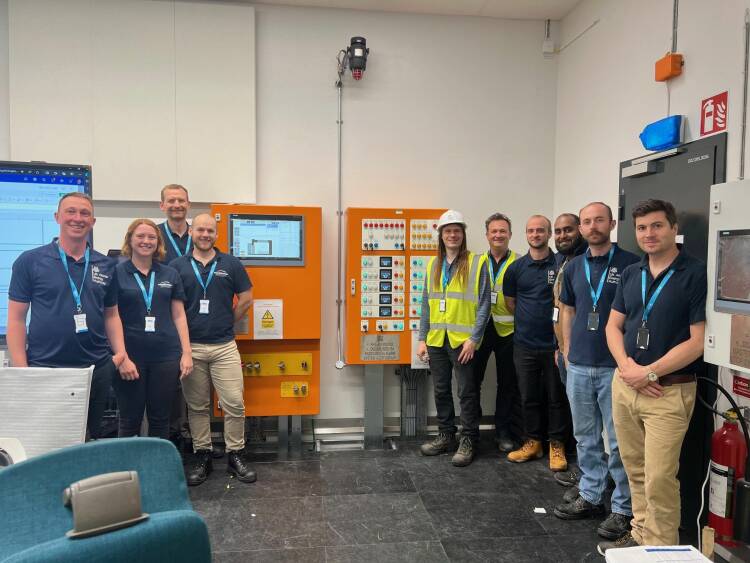