The Lasers4MaaS (Lasers-for-Manufacturing-as-a-Service) project, funded by a European Union HORIZON grant of approximately £6.7 million, commenced with a launch event held in January 2025. The project's objective is to integrate advanced laser welding technologies with digital platforms, facilitating flexible, scalable, and sustainable production solutions.
Lasers4MaaS aims to address the pressing need for sustainable and efficient manufacturing solutions. It will build on the concept of servitisation of manufacturing resources to produce on-demand customised products with high quality, flexibility and short lead times.
Driving Down Costs and Boosting Efficiency Across Multiple Sectors
The project has the potential to revolutionise laser welding across various sectors including but not limited to renewable energy such as hydrogen and fusion energy, automotive, food packaging, and aerospace.
For example, fast remote laser welding processes, capable of producing high-quality service pipe joints in extreme environments, would enhance the maintainability of future fusion power plants. The UK Atomic Energy Authority’s centre for Remote Applications in Challenging Environments will provide a use case for the project’s technological development, identifying, clarifying and organising the needs of end users in fusion energy.
The objectives of the fusion energy use case are as follows:
Reduction in maintenance costs: Enabling unmanned monitoring and maintenance in restricted areas such as service pipes in fusion machines.
Reduction in weld defects: Leveraging the latest Machine Learning (ML) and Artificial Intelligence (AI) along with sensor fusion and physics-informed ML and AI.
Functional improvement: Controlling and modifying the weld profile and microstructure during solidification through conditioning the materials. This will accelerate efficient utilisation of materials and help increase the welding speed.
Dr Robert Skilton, Robotics Fellow and Head of Robotics Research & Technology at UKAEA, said:
“As experts in fusion robotics technology, we are pleased to participate in this HORIZON project with our partners, which has the potential to make a significant impact across diverse sectors through the application of cutting-edge technology.”
Advancing Laser Welding Technology: Key Innovations
Key innovations will include the deployment of dynamic beam shaping, AI-driven manufacturing, digital manufacturing platforms, and sustainable and decentralised manufacturing, which offer benefits like enhanced flexibility and precision, seamless data integration for real-time monitoring, quality control, and predictive maintenance.
The current technological readiness level (TRL) of advanced manufacturing technologies is TRL 4, where it is at basic validation in a laboratory environment. The project aims to increase this to TRL 6, which tests the technology in a relevant operational environment, ensuring readiness for real-world applications. The project is planned for completion in 2028.
Academia and Industry Unite for Breakthrough Innovations
Coordinated by WMG, a department at the University of Warwick, the project brings together an international consortium of leading academics and industry experts. The project is also supported by an industrial advisory board and is seeking and accepting new members.
The open-day event was hosted by WMG, The University of Warwick, focussing on dynamic beam shaping for high power laser beam welding, one of the core innovations of Lasers4MaaS.
Pasquale Franciosa, Lases4MaaS Project Coordinator and Head of the Laser Beam Welding Group at WMG, The University of Warwick, said:
“The deployment of dynamic beam shaping within laser welding has an immense potential for servitisation. Manufacturers will be able to build products on-demand, without the need of re-investment in new equipment, thereby enabling rapid repurposing,”
Lasers4MaaS Takes Off:Pioneering AI-Powered Laser Welding for Renewable Energy and Beyond
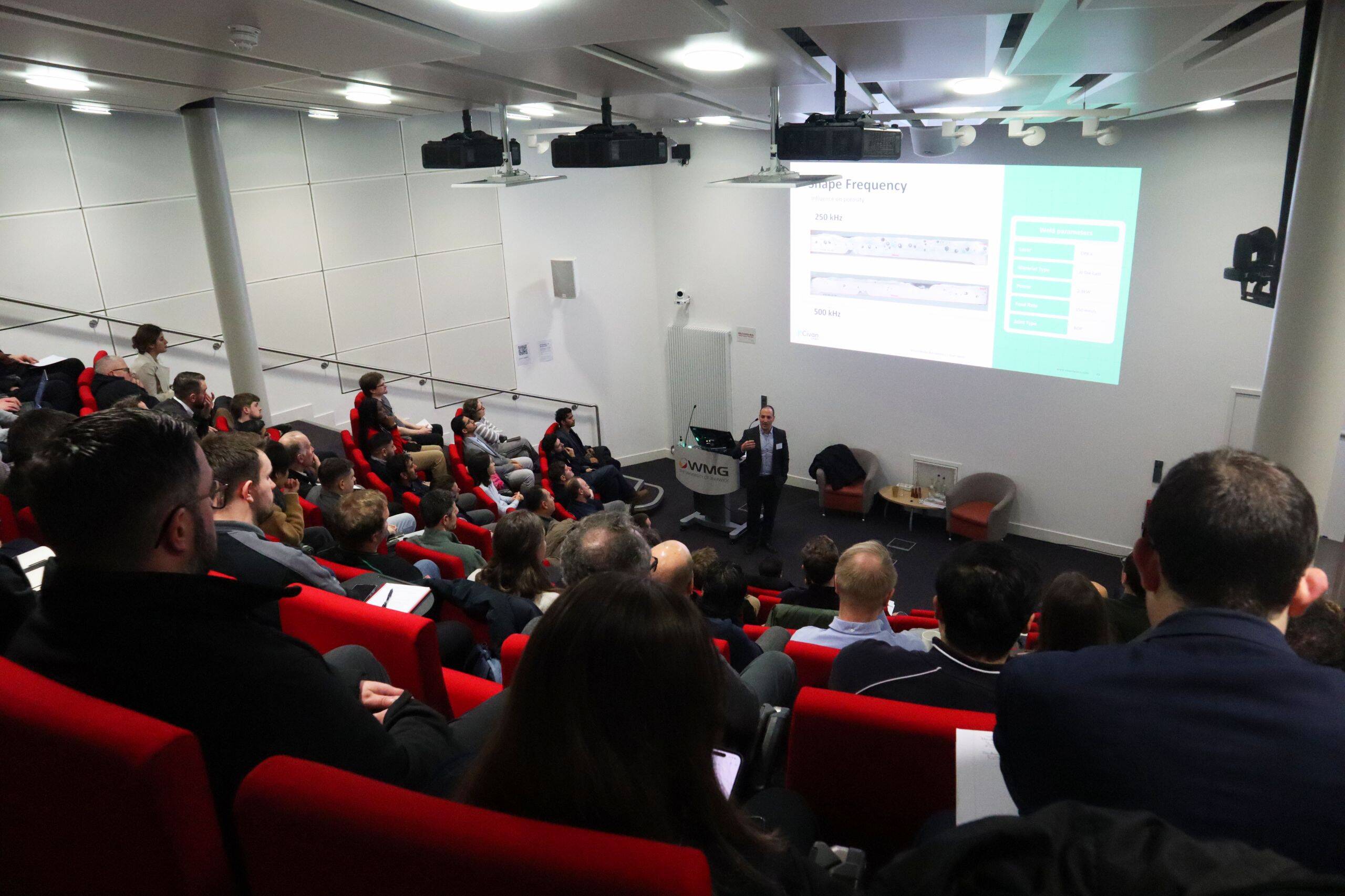
The Lasers4MaaS (Lasers-for-Manufacturing-as-a-Service) project, funded by a European Union HORIZON grant of approximately £6.7 million, commenced with a launch event held in January 2025. The project's objective is to integrate advanced laser welding technologies with digital platforms, facilitating flexible, scalable, and sustainable production solutions.
Lasers4MaaS aims to address the pressing need for sustainable and efficient manufacturing solutions. It will build on the concept of servitisation of manufacturing resources to produce on-demand customised products with high quality, flexibility and short lead times.
Driving Down Costs and Boosting Efficiency Across Multiple Sectors
The project has the potential to revolutionise laser welding across various sectors including but not limited to renewable energy such as hydrogen and fusion energy, automotive, food packaging, and aerospace.
For example, fast remote laser welding processes, capable of producing high-quality service pipe joints in extreme environments, would enhance the maintainability of future fusion power plants. The UK Atomic Energy Authority’s centre for Remote Applications in Challenging Environments will provide a use case for the project’s technological development, identifying, clarifying and organising the needs of end users in fusion energy.
The objectives of the fusion energy use case are as follows:
Reduction in maintenance costs: Enabling unmanned monitoring and maintenance in restricted areas such as service pipes in fusion machines.
Reduction in weld defects: Leveraging the latest Machine Learning (ML) and Artificial Intelligence (AI) along with sensor fusion and physics-informed ML and AI.
Functional improvement: Controlling and modifying the weld profile and microstructure during solidification through conditioning the materials. This will accelerate efficient utilisation of materials and help increase the welding speed.
Dr Robert Skilton, Robotics Fellow and Head of Robotics Research & Technology at UKAEA, said:
“As experts in fusion robotics technology, we are pleased to participate in this HORIZON project with our partners, which has the potential to make a significant impact across diverse sectors through the application of cutting-edge technology.”
Advancing Laser Welding Technology: Key Innovations
Key innovations will include the deployment of dynamic beam shaping, AI-driven manufacturing, digital manufacturing platforms, and sustainable and decentralised manufacturing, which offer benefits like enhanced flexibility and precision, seamless data integration for real-time monitoring, quality control, and predictive maintenance.
The current technological readiness level (TRL) of advanced manufacturing technologies is TRL 4, where it is at basic validation in a laboratory environment. The project aims to increase this to TRL 6, which tests the technology in a relevant operational environment, ensuring readiness for real-world applications. The project is planned for completion in 2028.
Academia and Industry Unite for Breakthrough Innovations
Coordinated by WMG, a department at the University of Warwick, the project brings together an international consortium of leading academics and industry experts. The project is also supported by an industrial advisory board and is seeking and accepting new members.
The open-day event was hosted by WMG, The University of Warwick, focussing on dynamic beam shaping for high power laser beam welding, one of the core innovations of Lasers4MaaS.
Pasquale Franciosa, Lases4MaaS Project Coordinator and Head of the Laser Beam Welding Group at WMG, The University of Warwick, said:
“The deployment of dynamic beam shaping within laser welding has an immense potential for servitisation. Manufacturers will be able to build products on-demand, without the need of re-investment in new equipment, thereby enabling rapid repurposing,”
Lasers4MaaS Takes Off:Pioneering AI-Powered Laser Welding for Renewable Energy and Beyond
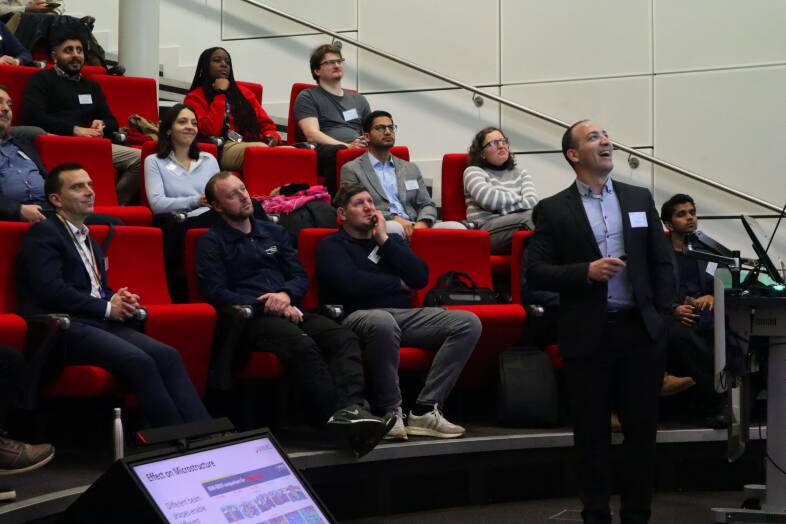