
Can you share a project you’ve worked on recently that showcases innovation in materials science?
A major challenge with coatings is ensuring they stay bonded to components during temperature changes. When a coated steel pipe is heated, the steel expands much more than the coating, which can cause the coating to crack. To address this, we’ve used an interlayer and dopants within the coating to improve thermal cycling stability. We recently tested these coatings at the Dalton Cumbrian Facility, irradiating them with heavy ions as a surrogate for neutron irradiation. The interlayers and doping helped maintain the coatings' stability under irradiation, preserving their crystal structure. This is crucial because changes in crystal structure can lead to cracking and reduced permeation performance. The results are promising, and I’m excited to see how these coatings perform in permeation tests.
Can you describe a project where collaboration played a key role in achieving success?
Collaboration is key! I work with external coating suppliers to ensure our developments are scalable and applicable beyond the lab. We also collaborate internationally, such as with IPP Garching in Germany, building on their expertise in deuterium interactions with irradiation damage in bulk tungsten, and extending it to tungsten coatings and ceramic coatings. Additionally, we are sending coatings to Romania for tritium exposure with Tritium Fuel Cycle division at UKAEA and planning tritium permeation experiments with the Canadian Nuclear Laboratory. These samples will be analysed with atom probe tomography (APT) to map the tritium inside them, as part of a development program aimed at advancing the use of APT to study hydrogen isotopes. The data gathered from APT and complementary techniques will be used by the tritium modelling team at UKAEA to validate tritium inventory models that are needed to ensure we can achieve sustainable fusion energy.
What advice would you give to someone starting out in materials engineering?
Talk to people, work with people and share ideas as much as you can. Not only will it be super interesting and fun, but it also is a great way to make the best use of your own and other people’s knowledge. You will be building your area of expertise, which you can share and contribute to collaborations, but you can also make the most of other peoples’ insights, specialist skillsets and different points of view.
Please check our website for details of what’s going on, or email marketing@ukaea.uk for information.
Can you introduce yourself and your role within UKAEA?
My name is Hazel Gardner, and I am a Senior Materials Engineer in the Materials division at UKAEA. I head up the coatings programme, developing tritium permeation barriers and corrosion barriers that can be used in the breeder blanket of future fusion devices. The permeation barriers help prevent tritium loss within the breeder blanket, ensuring the tritium is available for use as fuel and supporting safe powerplant maintenance and operation. In some cases, a topcoat is needed to protect the permeation barrier from corrosion.
My team works with industry to produce coatings, which we then, based on the findings, optimise to improve their performance. The aim is to develop a coating that reduces tritium permeation while staying well-adhered to the substrate under thermal cycling and irradiation.
What inspired you to pursue a career in materials engineering, and how did you find your way to UKAEA?
I studied materials science as an undergrad and enjoyed its interdisciplinary nature. Hands-on lab experience through summer projects and my Masters inspired me to continue researching.
I enjoy working on projects with clear real-world applications and my PhD focused on aerospace materials, using atom probe tomography to study how oxygen affects titanium fan blades in jet engines, sponsored by Rolls Royce. I often work at the nanoscale and enjoyed both the detailed focus as well the chance to see the bigger picture, such as visiting the engine build line in Derby.
After my PhD, I worked as a postdoc developing oxide dispersion strengthened nickel alloys for molten salt fission reactors, using atom probe to characterise the oxide particles. This was my first experience with nuclear materials, collaborating with US researchers during COVID-19. When the job at UKAEA came up, it was a great chance to apply my experience with materials in extreme environments from aerospace and fission to the materials science challenges facing fusion energy.
This month we had the pleasure of speaking with Hazel Gardner, Senior Materials Engineer, who shared insights into her role and what inspired her to pursue materials enginering.
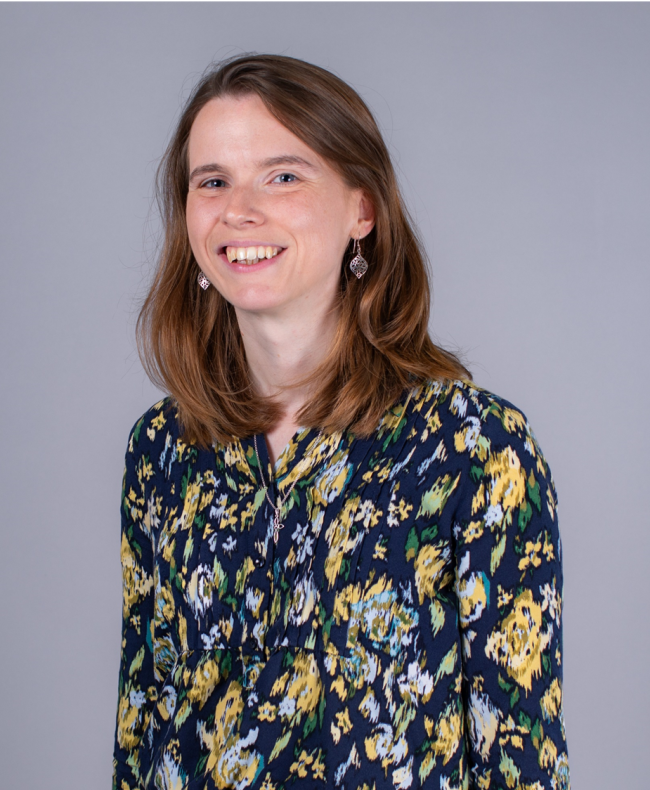
Can you share a project you’ve worked on recently that showcases innovation in materials science?
A major challenge with coatings is ensuring they stay bonded to components during temperature changes. When a coated steel pipe is heated, the steel expands much more than the coating, which can cause the coating to crack. To address this, we’ve used an interlayer and dopants within the coating to improve thermal cycling stability. We recently tested these coatings at the Dalton Cumbrian Facility, irradiating them with heavy ions as a surrogate for neutron irradiation. The interlayers and doping helped maintain the coatings' stability under irradiation, preserving their crystal structure. This is crucial because changes in crystal structure can lead to cracking and reduced permeation performance. The results are promising, and I’m excited to see how these coatings perform in permeation tests.
Can you describe a project where collaboration played a key role in achieving success?
Collaboration is key! I work with external coating suppliers to ensure our developments are scalable and applicable beyond the lab. We also collaborate internationally, such as with IPP Garching in Germany, building on their expertise in deuterium interactions with irradiation damage in bulk tungsten, and extending it to tungsten coatings and ceramic coatings. Additionally, we are sending coatings to Romania for tritium exposure with Tritium Fuel Cycle division at UKAEA and planning tritium permeation experiments with the Canadian Nuclear Laboratory. These samples will be analysed with atom probe tomography (APT) to map the tritium inside them, as part of a development program aimed at advancing the use of APT to study hydrogen isotopes. The data gathered from APT and complementary techniques will be used by the tritium modelling team at UKAEA to validate tritium inventory models that are needed to ensure we can achieve sustainable fusion energy.
What advice would you give to someone starting out in materials engineering?
Talk to people, work with people and share ideas as much as you can. Not only will it be super interesting and fun, but it also is a great way to make the best use of your own and other people’s knowledge. You will be building your area of expertise, which you can share and contribute to collaborations, but you can also make the most of other peoples’ insights, specialist skillsets and different points of view.
Please check our website for details of what’s going on, or email marketing@ukaea.uk for information.
I enjoy working on projects with clear real-world applications and my PhD focused on aerospace materials, using atom probe tomography to study how oxygen affects titanium fan blades in jet engines, sponsored by Rolls Royce. I often work at the nanoscale and enjoyed both the detailed focus as well the chance to see the bigger picture, such as visiting the engine build line in Derby.
After my PhD, I worked as a postdoc developing oxide dispersion strengthened nickel alloys for molten salt fission reactors, using atom probe to characterise the oxide particles. This was my first experience with nuclear materials, collaborating with US researchers during COVID-19. When the job at UKAEA came up, it was a great chance to apply my experience with materials in extreme environments from aerospace and fission to the materials science challenges facing fusion energy.
Can you introduce yourself and your role within UKAEA?
My name is Hazel Gardner, and I am a Senior Materials Engineer in the Materials division at UKAEA. I head up the coatings programme, developing tritium permeation barriers and corrosion barriers that can be used in the breeder blanket of future fusion devices. The permeation barriers help prevent tritium loss within the breeder blanket, ensuring the tritium is available for use as fuel and supporting safe powerplant maintenance and operation. In some cases, a topcoat is needed to protect the permeation barrier from corrosion.
My team works with industry to produce coatings, which we then, based on the findings, optimise to improve their performance. The aim is to develop a coating that reduces tritium permeation while staying well-adhered to the substrate under thermal cycling and irradiation.
What inspired you to pursue a career in materials engineering, and how did you find your way to UKAEA?
I studied materials science as an undergrad and enjoyed its interdisciplinary nature. Hands-on lab experience through summer projects and my Masters inspired me to continue researching.
This month we had the pleasure of speaking with Hazel Gardner, Senior Materials Engineer, who shared insights into her role and what inspired her to pursue materials enginering.