Four innovative organisations have been supported by the UKAEA to develop a range of engineering solutions that could help to deliver fusion energy for future generations.
The organisations – three of which are based in Sheffield – have received funding and support over the past year through UKAEA’s Fusion Futures, a four-year programme that aims to foster world-leading innovation whilst stimulating industry capacity through international collaboration. The Fusion Futures Industry Capability initiative focuses on generating new capability and capacity in the UK supply chain, supporting the UK’s position as a world leader in sustainable fusion energy.
Fusion Futures has enabled each participating organisation to develop manufacturing technologies that could enhance the designs of future fusion power plants such as the Spherical Tokamak for Energy Production (STEP) programme to design and build the UK’s first prototype fusion energy power plant in Nottinghamshire.
Stephen Wheeler, UKAEA Executive Director, said:
“These crucial Fusion Futures projects enhance industry capability within the growing UK fusion sector whilst supporting SMEs to work together on innovative solutions that will serve the local economy and wider fusion ecosystem now and in the future.”
John Schofield, Founder and CEO of Acantecs said:
“Acantecs is proud to have participated in the UK Fusion Futures programme. This collaboration has offered a valuable opportunity to explore
innovative applications of our existing technologies. By integrating electroforming as a complementary method of canister manufacturing alongside our established PM HIP technology and processes, we have opened a new pathway for near-net shape product production. This advancement not only supports the evolving needs of future fusion technologies but also highlights the power of collaborative innovation.”
Andy Bushby, Ultima Forma's Chief Technology Officer, said:
"Ultima Forma, in close collaboration with Acantecs and AML, are pleased to have brought the future of fusion a step closer with this project to produce reactor components by near net-shaped HIP processing with electroformed canisters."
Richard Mincher, Founder and CEO at FORG3D, said:
“FORG3D is thrilled to be working with the UK Atomic Energy Authority as part of the Fusion Futures programme. It's been a fantastic opportunity to collaborate with world-class experts and contribute to the future of clean energy. Programmes like Fusion Futures is exactly what's needed to connect ambitious startups like ours with national-scale impact. We're excited about where this could lead and proud to be playing a small part in the journey toward fusion energy.”
UKAEA’s Stephen Wheeler visiting FORG3D team in Sheffield
Acantecs, AML and Ultima Forma visiting RTC in Sheffield with UKAEA’s Stephen Wheeler and Matt Stephenson
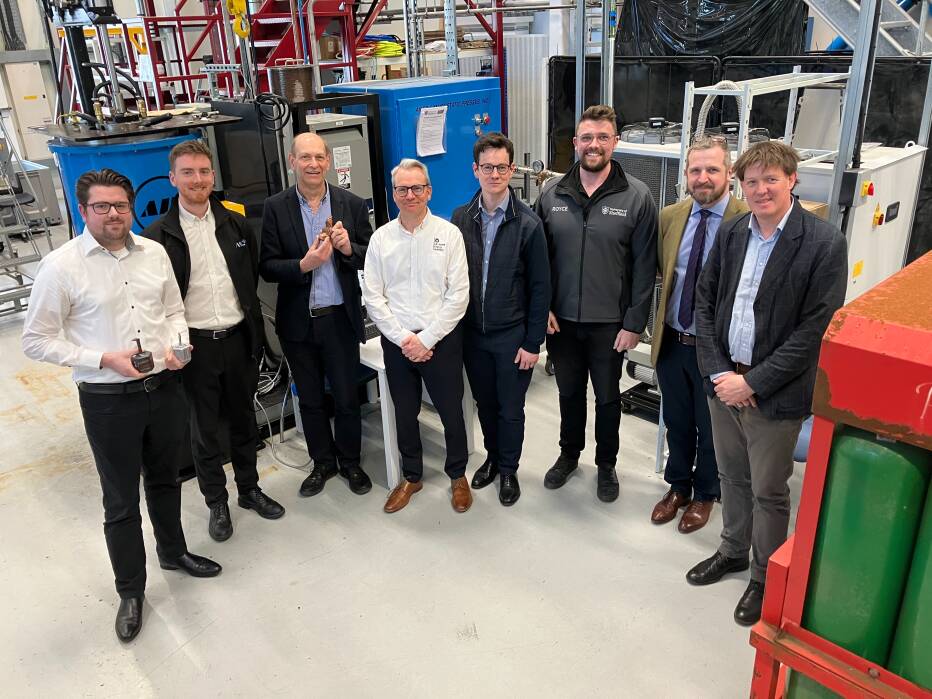
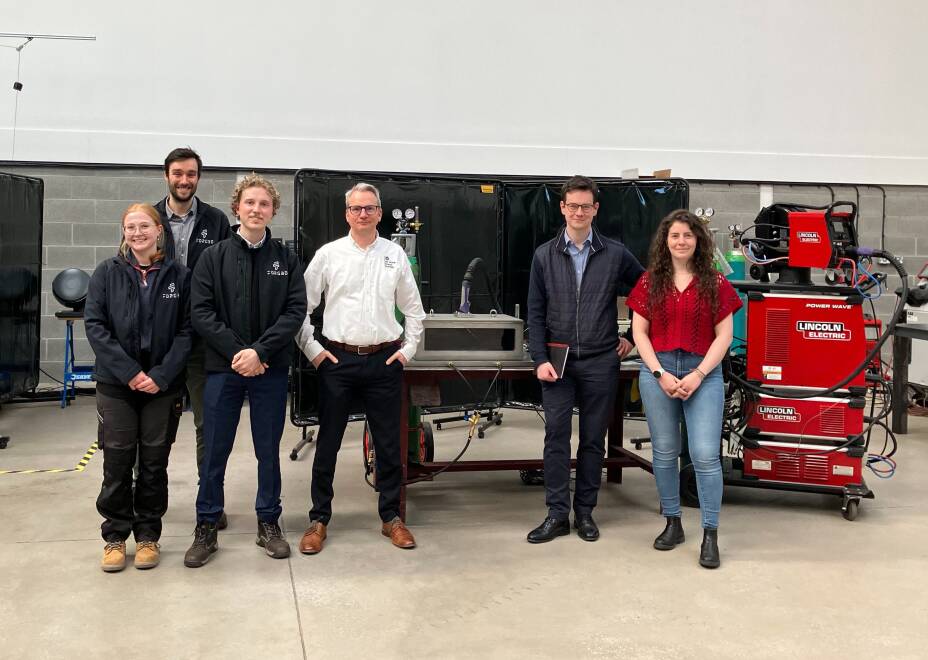
Acantecs and AML – both located in Sheffield – along with Ultima Forma – located in Basingstoke – form a consortium of advanced manufacturing companies. Through Fusion Futures, the companies are developing technologies to manufacture challenging fusion parts using materials such as tungsten, copper alloys, and other fusion grade steels, for heat sink and structural applications.
The technology, called hot isostatic pressing (HIP), can produce complex geometry, multi-material components. In this project, the innovative electroforming method was utilised to produce the near-net shape canisters required
for the HIP process.
Sheffield-based metal production specialist, FORG3D, has used Fusion Futures funding to develop a patented form of wire arc additive manufacturing for the in-situ repair of in-vessel tungsten components. The deployment of advanced repair technology like this will be essential for reliably and efficiently maintaining future fusion power plants.
Growing Our Industry for UK Fusion
Four innovative organisations have been supported by the UKAEA to develop a range of engineering solutions that could help to deliver fusion energy for future generations.
The organisations – three of which are based in Sheffield – have received funding and support over the past year through UKAEA’s Fusion Futures, a four-year programme that aims to foster world-leading innovation whilst stimulating industry capacity through international collaboration. The Fusion Futures Industry Capability initiative focuses on generating new capability and capacity in the UK supply chain, supporting the UK’s position as a world leader in sustainable fusion energy.
Fusion Futures has enabled each participating organisation to develop manufacturing technologies that could enhance the designs of future fusion power plants such as the Spherical Tokamak for Energy Production (STEP) programme to design and build the UK’s first prototype fusion energy power plant in Nottinghamshire.
Stephen Wheeler, UKAEA Executive Director, said:
“These crucial Fusion Futures projects enhance industry capability within the growing UK fusion sector whilst supporting SMEs to work together on innovative solutions that will serve the local economy and wider fusion ecosystem now and in the future.”
John Schofield, Founder and CEO of Acantecs said:
“Acantecs is proud to have participated in the UK Fusion Futures programme. This collaboration has offered a valuable opportunity to explore for the HIP process.
Sheffield-based metal production specialist, FORG3D, has used Fusion Futures funding to develop a patented form of wire arc additive manufacturing for the in-situ repair of in-vessel tungsten components. The deployment of advanced repair technology like this will be essential for reliably and efficiently maintaining future fusion power plants.
Andy Bushby, Ultima Forma's Chief Technology Officer, said:
"Ultima Forma, in close collaboration with Acantecs and AML, are pleased to have brought the future of fusion a step closer with this project to produce reactor components by near net-shaped HIP processing with electroformed canisters."
Richard Mincher, Founder and CEO at FORG3D, said:
“FORG3D is thrilled to be working with the UK Atomic Energy Authority as part of the Fusion Futures programme. It's been a fantastic opportunity to collaborate with world-class experts and contribute to the future of clean energy. Programmes like Fusion Futures is exactly what's needed to connect ambitious startups like ours with national-scale impact. We're excited about where this could lead and proud to be playing a small part in the journey toward fusion energy.”
Fusion power plants will operate under complex conditions, including extreme temperatures, high neutron loads and high magnetic fields. Developing highly specialised technologies that can operate under these extreme conditions is essential to making fusion energy a commercially viable part of the world’s energy mix.
UKAEA’s Stephen Wheeler visiting FORG3D team in Sheffield
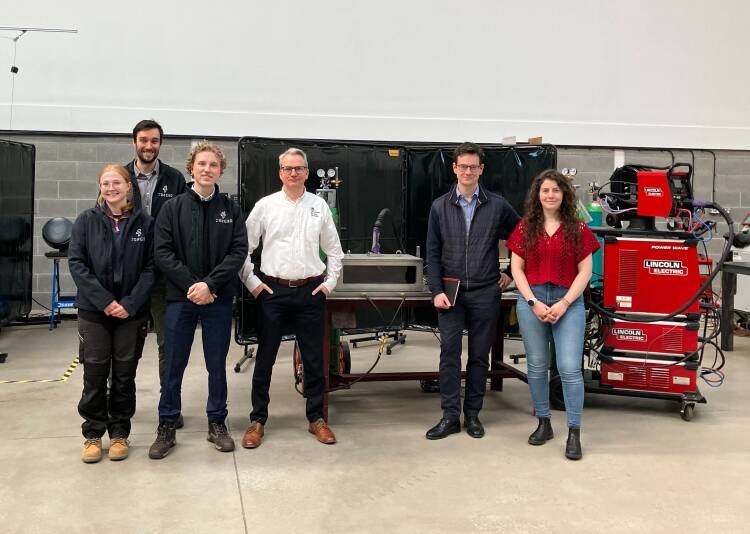
Acantecs, AML and Ultima Forma visiting RTC in Sheffield with UKAEA’s Stephen Wheeler and Matt Stephenson
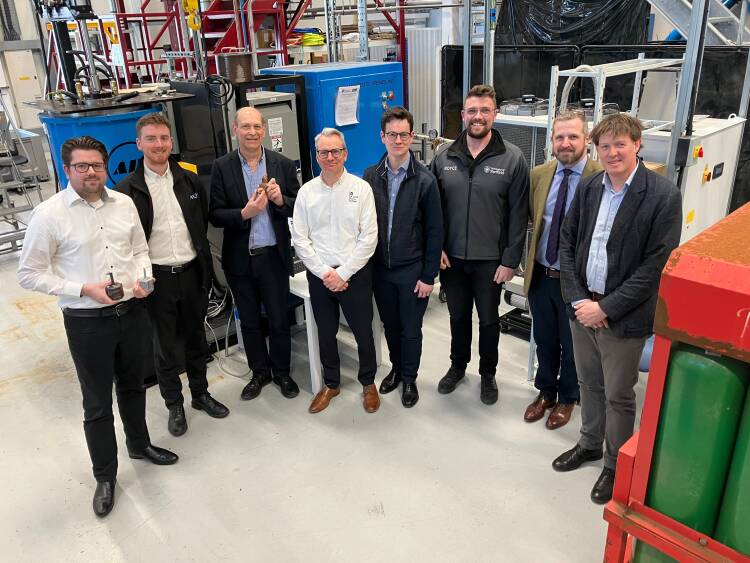
Acantecs and AML – both located in Sheffield – along with Ultima Forma – located in Basingstoke – form a consortium of advanced manufacturing companies. Through Fusion Futures, the companies are developing technologies to manufacture challenging fusion parts using materials such as tungsten, copper alloys, and other fusion grade steels, for heat sink and structural applications.
The technology, called hot isostatic pressing (HIP), can produce complex geometry, multi-material components. In this project, the innovative electroforming method was utilised to produce the near-net shape canisters required